How to protect and maintain plastic mold processing and production applications
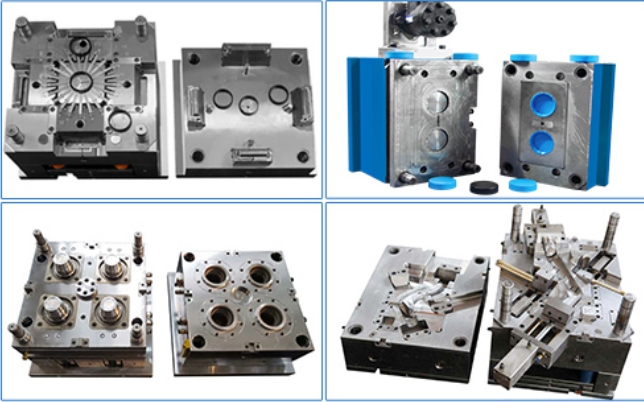
a:After long-term application in plastic mold processing, the cutting edge should be ground
It is necessary to demagnetize the edge surface after grinding, and it should not have magnetism, otherwise it is easy to cause material blockage. Plastic molds need to be recorded and calculated specifically for their use, maintenance (lubrication, cleaning, rust prevention), and damage. Based on this, it is possible to identify which parts and components have been damaged, the degree of wear, and provide information and data for discovering and solving problems, as well as the molding technology parameters and product materials of the plastic mold, in order to shorten the trial run time of the mold and improve production power. Under normal operation of the injection molding machine and mold, various functions of the plastic mold should be tested, and the standard amount of plastic parts ultimately formed should be measured. Based on this information, the existing situation of the mold can be determined, and the damage locations of the cavity, core, cooling system, and parting surface can be identified. Based on the information provided by the plastic parts, the damage situation of the plastic mold and repair methods can be determined.
b: Elastic parts such as plastic molds and springs are most susceptible to damage during use, usually exhibiting signs of cracking and deformation. The adopted method is replacement, and during the replacement process, attention must be paid to the specifications and types of springs. The specifications and types of springs are recognized through color, outer diameter, and length, and can only be replaced if all three are the same. The quality of imported springs is superior, and famous brands include Raymond mold springs.
How to protect and maintain plastic mold processing and production applications
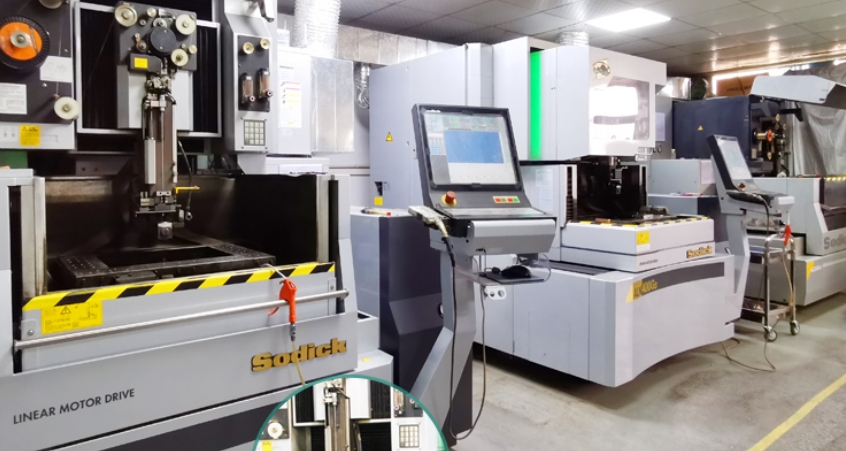
c: During the processing of plastic molds, the punch is prone to breakage, bending, and gnawing, and the punch sleeve is generally gnawed.
The damage to the punch and punch sleeve is usually replaced with the same standard parts. The parameters of the punch mainly include some standards for operation, some standards for equipment, and length standards.
d: Plastic mold fastening parts, check if the fastening parts are loose or damaged, and the adopted method is to replace them with parts of the same standard.
e: Plastic mold pressing parts such as pressure plates, Uni glue, etc., unloading parts such as strippers, pneumatic top materials, etc. During maintenance, check the connection and damage of various parts of the accessories, make corrections to some of the damaged parts, and inspect the pneumatic top material for any signs of air leakage. Adopt specific measures for specific situations. Replace if the trachea is damaged. Key point tracking inspection should be carried out on several important components of the mold: the function of the ejection and guide components is to ensure the opening and closing movement of the plastic mold and the ejection of the plastic part. If any part of it gets stuck due to hazards, it will cause production to stop. Therefore, it is necessary to regularly adhere to the lubrication of the plastic mold’s ejector pin and guide pillar (using the most suitable lubricant), and regularly check whether the ejector pin, guide pillar, etc. have undergone deformation and surface hazards. Once discovered, they should be replaced in a timely manner; After completing a production cycle, it is necessary to apply professional anti rust oil to the surface, movement, and guiding components of the mold operation. Special attention should be paid to protecting the elastic strength of the bearing parts of the mold with gears and racks, as well as the spring mold, to ensure that it is always in the best operating condition; As the production time continues, the cooling channel is prone to accumulation of scale, rust, sludge, and algae, resulting in a smaller cross-section of the cooling channel and narrower cooling channel, greatly reducing the heat exchange rate between the coolant and the mold, and increasing the company’s production costs. Therefore, the cleaning of the channel should be taken seriously; For hot runner molds, the maintenance of heating and control systems is particularly important as it helps to avoid production problems.