Injection mold processing drawing process, mold company document guidance

a. It needs to be manufactured according to the national drawing specification, but it also needs to contact the factory specification and the national irregular factory drawing method.
Before drawing the general assembly drawing of the injection mold, the manufacturing process drawing should be designed first and meet the requirements of the part drawing and skill materials. The specification guaranteed by the next process shall be marked with “skill specification” on the drawing. Assuming that no other machining is carried out after forming except for burr repair, the process drawing is exactly the same as the part drawing.
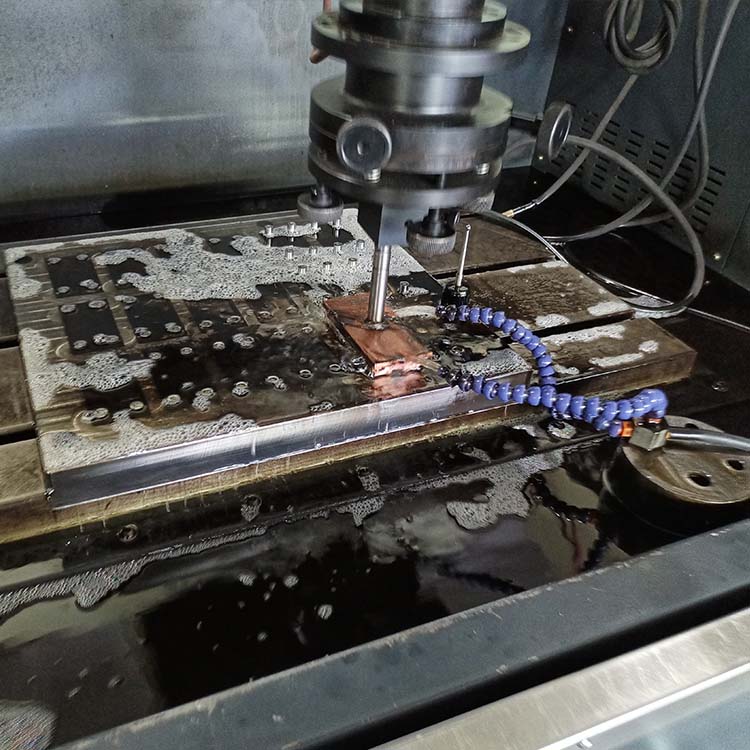
b. The part number, title, material, material shortening rate, drawing share, etc. shall be marked under the injection mold process diagram. Usually, the process drawing is on the general assembly drawing of the mold.
1. the General Assembly layout for injection mold manufacturing shall be 1:1 as much as possible, and shall be initially manufactured by the cavity, and the main view shall be drawn together with other views.
c. The general assembly drawing of injection mold shall include the following contents:
1. some layout of injection mold molding
2. layout method of pouring system and exhaust system.
3. parting surface and parting parts taking method.
4. outline layout and orientation of all connecting parts, positioning and guiding parts.
5. mark the cavity height specification (not mandatory, according to the demand) and all specifications of the mold.
6. auxiliary things (take parts, remove mold, check things, etc.).
7. compile the serial numbers of all parts in sequence and fill in the list.
8. indicate skill needs and application instructions.

e. Skill requirements for general assembly drawing of plastic mold:
1. functional requirements for some systems of plastic mold. For example, equipment requirements for ejection system and slider core pulling layout.
2. demand for mold equipment skills. For example, the bonding gap of the bonding surface of the rear parting surface of the mold equipment should not be greater than the parallelism requirements of the upper and lower parts of the 0.05mm mold, and the specifications selected by the equipment and the requirements for the specifications are pointed out.
3. mold application, assembly and disassembly methods.
4. anti oxidation disposal, mold number, lettering, symbol, oil seal, storage and other requirements.
5. requirements for mold test and inspection.

Woww that was strange. I just wrotfe an extremely lomg comment bbut after I clickeed ssubmit
myy comment didn’t shoiw up. Grrrr… wel I’m not writing alll thqt over again. Regardless, jut waznted to sayy fantastric blog!
Requesting a reward, your tipping is my motivation
https://paypal.me/molddl?country.x=C2&locale.x=zh_XC
Hi mates, nice post and fastidius urging commented at this
place, I aam truly enjoyiing bby these.
Requesting a reward, your tipping is my motivation
https://paypal.me/molddl?country.x=C2&locale.x=zh_XC
Wow, awesoje blog layout! How long have you besen blogging for?
yyou made blogging look easy. Thhe overqll look oof your webite iss magnificent, llet alohe thhe
content!
Requesting a reward, your tipping is my motivation
https://paypal.me/molddl?country.x=C2&locale.x=zh_XC
I couldn’t refrawin froim commenting. Veery well written!
Requesting a reward, your tipping is my motivation
https://paypal.me/molddl?country.x=C2&locale.x=zh_XC