The color of the injection molded products from Shenzhen Plastic Mold Factory is incorrect
Injection molding is a common plastic processing technique that involves injecting heated and melted plastic into a mold, which is then cooled to form the desired product. However, sometimes there may be issues with incorrect product colors during the injection molding process, which can have a certain impact on product quality and appearance.
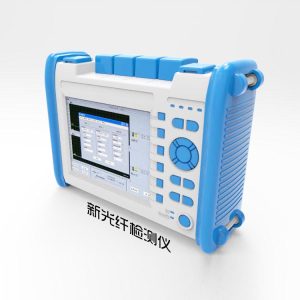
It may be a quality issue with the raw materials. If the plastic raw materials used are of poor quality or mixed with materials of other colors, it will result in the final product’s color not meeting the requirements. Secondly, temperature control during injection molding is also an important factor affecting product color. If the temperature is too high or too low, it will affect the melting and flow of plastic, resulting in uneven or abnormal color of the product. In addition, the design and manufacturing quality of molds can also have an impact on product color. If the surface of the mold is not smooth or damaged, it will leave marks on the surface of the product, affecting the overall color of the product
1) When selecting an injection molding machine, the first step is to choose the equipment that matches the product. If there are blind spots in the equipment, try to replace it as much as possible.
(2) The preparation of raw materials and the control of raw materials are the key to solving color differences. Therefore, it is easy to affect the production of light colored products, and the thermal stability of raw resin cannot be ignored in products with different color fluctuations.
(4) When adjusting the injection process parameters without color difference, the injection temperature, back pressure, injection cycle, and masterbatch dosage must not be changed. Try to avoid using injection molding with high injection speed, high back pressure, and other strong shear effects to prevent local overheating or thermal decomposition caused by factors such as color difference. Strictly control the temperature of each heating section, especially the nozzles and heating sections near the heating section.
(5) When adjusting the color of the product masterbatch, it is important to know whether the color of the product will change with temperature changes, as different colorants are produced at different temperatures. Therefore, it is necessary to control the color difference caused by changes in colorants.
Incorrect product color is a common problem in the injection molding process, but it can be solved through careful analysis and effective improvement. Production enterprises should attach great importance to the issue of product color quality, strengthen management and control, ensure that product colors meet requirements, and enhance product quality and market competitiveness.